Trees may become the key to ‘greener’ foam products
Made from wood pulp, they’re just as strong as Styrofoam — and work better at keeping things cold
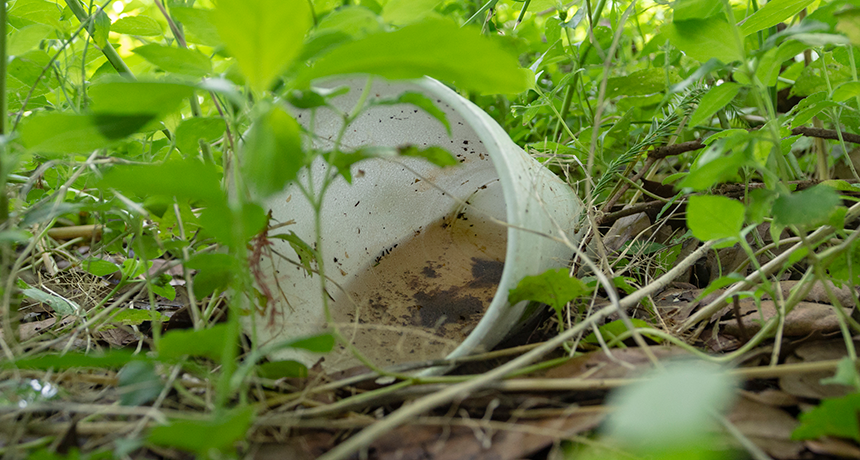
Unlike this Styrofoam cup, made from plastic, a new kind of foam is biodegradable.
tomschirtz/iStock/Getty Images Plus
If you’re heading to the beach on a hot summer day, you don’t want to forget the cooler full of drinks. You might load that cooler with ice. However, ice on its own won’t keep things cold for long. That’s why a cooler packs insulation in its walls. The best insulators have long been plastic-based foams, such as Styrofoam. But a new type of foam made from wood pulp works even better. And it’s friendlier to the environment.
Plastic foam is both incredibly useful and popular. Filled with millions of tiny air pockets, its frothy structure is both lightweight and strong. This material protects fragile packages during shipping. And when used as an insulator, plastic foam’s tiny bubbles help keep heat in — or out — for hours. That’s why people have relied on it for everything from cups and coolers to packaging and home insulation.
These foams have a few drawbacks, however. They are made from petroleum, a non-renewable material. And when someone has finished using these foam-based products, they’re difficult to recycle. Plastic foam doesn’t biodegrade (break down naturally). Instead, it tends to break apart into tiny little beads that can scatter on the wind, spreading pollution near and far.
That’s why researchers have been trying to find an alternative. They want something that’s “green” — better for the environment, both in how it’s made and how we get rid of it. Xiao Zhang and Amir Ameli are materials scientists who work at Washington State University in Richland. And they think the answer may lie in trees.
Turning to trees
Cellulose is the very sturdy material that makes up a plant’s cell walls. Other scientists had found ways to make foam from the cellulose in trees. They liked that the starting ingredient not only is a renewable resource, but also can break down completely in the environment.
However, straight from the plant, cellulose isn’t foamable. Earlier researchers had found they needed to first dissolve wood pulp with acid and then filter it. What remained would be tiny crystals of cellulose. They are so small that you need 500 of the crystals, side-by-side, to match the width of a human hair. These nanocrystals are the reason tree trunks are so strong.
To turn them into a foam, researchers dissolved the nanocrystals in harsh solvents. (Solvents are liquids that dissolve other substances.) Then they froze it to create a foam and dried it out to remove the solvent. But the resulting material was weaker than traditional plastic foams and didn’t insulate as well as Styrofoam. The cellulose products also broke down in hot and humid conditions.
Zhang and Ameli wanted to make something that not only worked better than plastic foams but also was friendlier to the environment. For instance, Ameli explains, “We wanted to avoid any harmful or expensive solvents.”
“Cellulose is soluble in water,” he notes. His team then chose other ingredients that would dissolve in water. Now, when they removed water from the solution, the team hoped to end up with a strong cellulose foam.
The researchers prepared different recipes. Some were just a mix of cellulose nanocrystals and water. For stretchiness, other recipes contained a polymer known as polyvinyl alcohol. Still others used all of those ingredients, plus an acid. That acid helped the molecules of cellulose and polyvinyl alcohol bond. Those bonds “hold the nanoscale ingredients together and make the material stronger,” Ameli explains. Stronger materials create smaller bubbles inside the foam, he adds, which should produce a higher-quality foam.
Next, the researchers poured each mix into a tube and froze it for six hours. That kept the nanocrystals in place. Once each mixture was good and solid, they freeze-dried it. This removed the water, leaving behind just the foam.
Pulp power
The team then compared how well each foam performed. They also looked at a thin slice of each foam under a scanning electron microscope to see its tiny air pockets. Air spaces in the cellulose-only foam were big — more than 0.2 millimeter (0.008 inch) across. The polyvinyl alcohol and acid recipe left much smaller pockets. These bubbles were less than half as big. They also were evenly distributed in the foam. That suggested this foam should be stronger.
Sure enough, when the researchers tested the foams by putting weights atop them, the acid foam stood up to much more pressure than either the cellulose-only or the cellulose-and-alcohol foams. The acid foam should therefore work well for packaging.
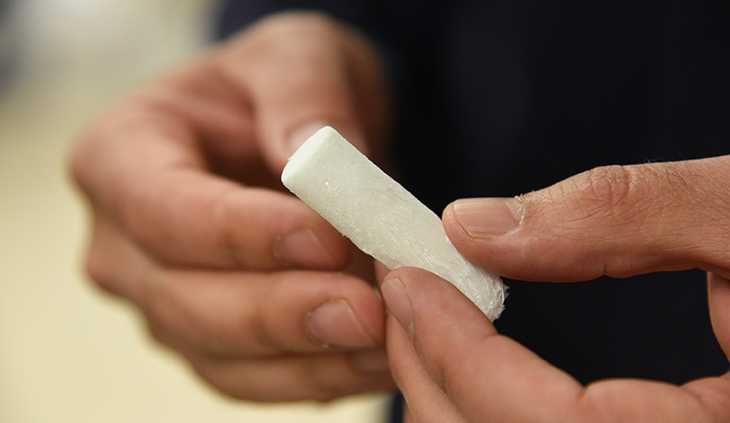
Finally, the researchers tested how well the foams kept heat in (or out). Once again, the acid recipe proved the clear winner. This foam prevented heat from moving through it much better than the other types they’d made. It also insulated better than Styrofoam. And that’s because it had so many tiny bubbles, Ameli says. “As the bubbles get smaller and smaller, air cannot freely move inside the bubble, and cannot transfer heat as quickly.”
The researchers describe their findings in the August 15 issue of Carbohydrate Polymers.
The team has not yet studied how well the foam will break down in the environment. But Ameli expects it should degrade quickly.
Until the foam’s ability to break down has been tested, it should stay in the lab, says Monica Ferreira da Costa. She is an oceanographer at the Federal University of Pernambuco in Brazil. Da Costa studies plastic pollution in the world’s oceans. She argues that before replacements for plastic foams are made widely available, researchers need to be certain they won’t just create some new type of pollution.
“I don’t believe any product should ever enter the market again” without thorough testing first, Costa says. “There is no need to repeat the same mistakes over and over again.”
This is one in a series presenting news on technology and innovation, made possible with generous support from the Lemelson Foundation.